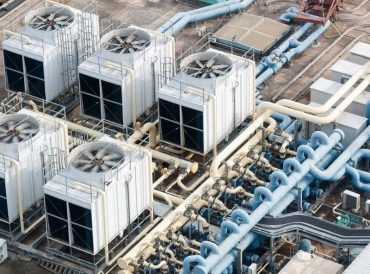
Cleanroom HVAC in KSA: Key Guide to Advanced Contamination Control
Introduction to Cleanroom HVAC Systems in KSA
In the Kingdom of Saudi Arabia (KSA), industries such as pharmaceuticals, electronics, aerospace, and healthcare require highly controlled environments to maintain stringent quality standards. Cleanroom HVAC systems are crucial in achieving contamination control by regulating temperature, humidity, airflow, and airborne particles. Properly designed HVAC systems ensure compliance with ISO standards, GMP (Good Manufacturing Practices), and local regulations.
Key Components of Cleanroom HVAC Systems
1. High-Efficiency Air Filtration
Cleanrooms rely on HEPA (High-Efficiency Particulate Air) and ULPA (Ultra-Low Penetration Air) filters to remove contaminants. These filters effectively eliminate 99.97% to 99.9995% of airborne particles as small as 0.12 microns, ensuring a contaminant-free environment.
2. Airflow and Ventilation Design
Cleanrooms in KSA employ laminar airflow (unidirectional) or turbulent airflow (non-unidirectional) depending on the required cleanliness level.
- Laminar flow systems are common in ISO Class 1-5 cleanrooms, ensuring air moves in a uniform direction at a consistent speed.
- Turbulent flow systems are used in ISO Class 6-9 cleanrooms, where air is randomly distributed for less stringent cleanliness requirements.
3. Temperature and Humidity Control
Maintaining optimal temperature and relative humidity is critical for product stability and personnel comfort. Cleanroom HVAC systems regulate humidity levels between 30-60% and temperatures ranging from 18°C to 24°C, depending on industry requirements.
4. Pressure Differentials
To prevent contamination, cleanrooms maintain positive or negative pressure differentials:
- Positive-pressure cleanrooms prevent external contaminants from entering, ideal for pharmaceutical and semiconductor industries.
- Negative pressure cleanrooms contain hazardous materials within, used in biological laboratories and pharmaceutical compounding areas.
Compliance with Cleanroom Standards in KSA
ISO Classification and GMP Regulations
Cleanroom HVAC systems must comply with ISO 14644-1 classifications, which define cleanliness levels based on allowable particle counts. The common classes are:
- ISO Class 1-3: Ultra-clean environments for semiconductor and nanotechnology applications.
- ISO Class 4-6: Controlled environments for pharmaceutical production and biotechnology.
- ISO Class 7-9: Suitable for industries like food processing and general manufacturing.
Additionally, industries must adhere to Good Manufacturing Practices (GMP) and Saudi Food & Drug Authority (SFDA) regulations.
Energy Efficiency in Cleanroom HVAC Systems
1. Variable Air Volume (VAV) Systems
VAV systems adjust airflow based on real-time demand, significantly reducing energy consumption and operational costs compared to constant air volume (CAV) systems.
2. Heat Recovery Systems
Utilizing heat exchangers and energy recovery ventilators (ERVs) helps reclaim energy from exhaust air, improving efficiency while maintaining air quality.
3. Smart HVAC Controls
Advanced automation and IoT-based controls optimize performance by monitoring temperature, humidity, and airflow in real time, ensuring compliance with industry regulations while reducing energy wastage.
Challenges in Cleanroom HVAC Design and Maintenance
1. High Initial Investment
The cost of installing a cleanroom HVAC system can be substantial due to specialized equipment, filtration systems, and compliance requirements.
2. Stringent Maintenance Requirements
Regular filter replacement, airflow validation, and microbial contamination checks are necessary to maintain cleanroom integrity.
3. Adapting to KSA’s Harsh Climate
Saudi Arabia’s extreme heat and humidity require robust insulation, precise temperature control, and additional cooling capacity to ensure HVAC efficiency.
Best Practices for Cleanroom HVAC System Optimization
1. Regular HVAC Performance Testing
Conducting airflow velocity tests, filter integrity checks, and differential pressure monitoring ensures continuous compliance with ISO and GMP standards.
2. Implementing Energy-Efficient Technologies
Using EC (Electronically Commutated) fans, energy-efficient chillers, and LED lighting reduces operational costs and carbon footprint.
3. Training Personnel on Cleanroom Protocols
Staff training on proper gowning procedures, contamination control, and emergency response is critical for maintaining a contamination-free environment.
Conclusion
Investing in a high-quality Cleanroom HVAC system in KSA is essential for industries that require strict contamination control. By focusing on filtration efficiency, airflow design, regulatory compliance, and energy-saving solutions, businesses can achieve optimal performance while reducing operational costs. Adopting best practices in maintenance, monitoring, and technology upgrades ensures long-term reliability and compliance with international standards.